耐磨涂層后期磨削加工及其注意事項
2015-2-24 10:21:26 點擊:
摘要:涂層是做為耐磨材料的一種重要組成部分,且多數(shù)用于較精密的結(jié)構(gòu)件上,因此需要后期加工,本文介紹了加工工藝及加工注意事項。
對于耐磨涂層后期加工來講,磨削是唯一切實可行的精加工方法。由于涂層顆粒之間的結(jié)合主要依靠機械鑲嵌結(jié)合,且含有一定的孔隙,從磨削的觀點看,熱的轉(zhuǎn)移比較緩慢,常規(guī)致密材料的磨削加工方法并不適用于涂層材料的磨削加工。如果磨削壓力過大或速度過快,可能造成涂層表面顆粒發(fā)生轉(zhuǎn)移或被移動,從而導致涂層內(nèi)部顆粒發(fā)生脫落,甚至導致整個涂層從基體剝離。決定磨削加工工藝方法的因素包括:涂層類型、工件形狀、要求光潔度和公差等。
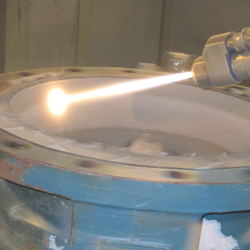
圖(1)是碳化鎢涂層噴涂作業(yè)現(xiàn)場
對于耐磨涂層后期加工來講,磨削是唯一切實可行的精加工方法。由于涂層顆粒之間的結(jié)合主要依靠機械鑲嵌結(jié)合,且含有一定的孔隙,從磨削的觀點看,熱的轉(zhuǎn)移比較緩慢,常規(guī)致密材料的磨削加工方法并不適用于涂層材料的磨削加工。如果磨削壓力過大或速度過快,可能造成涂層表面顆粒發(fā)生轉(zhuǎn)移或被移動,從而導致涂層內(nèi)部顆粒發(fā)生脫落,甚至導致整個涂層從基體剝離。決定磨削加工工藝方法的因素包括:涂層類型、工件形狀、要求光潔度和公差等。
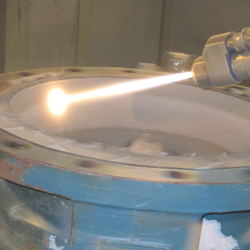
圖(1)是碳化鎢涂層噴涂作業(yè)現(xiàn)場
一般來講,噴涂粉末越細、涂層孔隙率越低、涂層越均勻,磨削加工后的光潔度越好。
選擇砂輪時應考慮涂層種類、硬度、工件大小與形狀、磨削量、表面光潔度要求、磨床類型等因素。一般遵循以下原則:
(1)盡可能選用最銳利的砂輪,這種砂輪切削速度快,不易過熱。砂輪銳利程度與砂輪所用磨粒的類型及粒度有關(guān)。對于磨削耐磨涂層的砂輪來講,常用的磨粒是碳化硅和金剛石。這是因為碳化硅磨粒在磨削時發(fā)生破裂后會呈現(xiàn)新的銳利的切削刃,而金剛石磨粒具有良好的耐久性,能干凈地磨削各種硬質(zhì)耐磨涂層。當磨粒粒度較小時,不僅具有較小的表面積,而且切削刃較銳利,比粗磨粒更容易陷入涂層內(nèi)部,從而獲得較高的光潔度。一般來講,用于耐磨涂層粗磨的磨粒粒度在125-150目,用于細磨的粒度在380-400目。
(2)所選砂輪內(nèi)部結(jié)構(gòu)及其硬度級別要能夠提供自由磨削的效果。砂輪內(nèi)部結(jié)構(gòu)是指砂輪內(nèi)部各個磨粒之間的間距,具有多孔結(jié)構(gòu)的砂輪,其磨削效果更佳,這是由于顆粒間造成的間隙能夠提供更大的存屑空隙造成的。砂輪硬度不同也會影響耐磨涂層磨削效果,較硬砂輪比較軟砂輪具有更長的使用壽命。當磨削應力較小、接觸面積較大及磨削速度較高時,推薦采用較軟的砂輪;當磨削應力較大、光潔度要求較高、接觸面積較小及砂輪較窄時,推薦采用較硬砂輪。
(3)選擇最適合的砂輪粘結(jié)類型。常用砂輪粘結(jié)劑有兩種,即陶瓷粘結(jié)劑和樹脂粘結(jié)劑。采用陶瓷粘結(jié)劑的砂輪能夠承受較高的磨削速度和精確的配合公差,且不受水、酸、油及溫度變化的影響,但要求磨床轉(zhuǎn)速要小于砂輪的安全操作速度,一般小于33米/秒。而采用樹脂粘結(jié)劑的砂輪,可用于更高的磨削速度,并產(chǎn)生更高的光潔度。
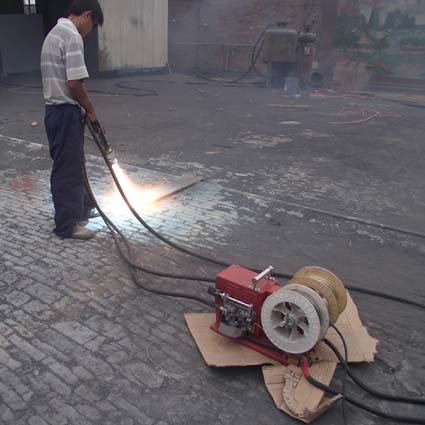
圖(2)是電弧噴涂防磨處理施工現(xiàn)場
圖(2)是電弧噴涂防磨處理施工現(xiàn)場
針對KN-75噴涂的WC類耐磨涂層,推薦磨削工藝如下:
1) 采用精密、高質(zhì)量的磨削設(shè)備;
2) 選用水溶性冷卻介質(zhì)淋洗;
3) 選用樹脂粘結(jié)金剛石砂輪,當工件外徑小于50mm時,選用φ500的砂輪;當工件外徑大于50mm時,選用φ762的砂輪;
4) 采用兩步法進行磨削,第一步:進行粗磨,其磨削參數(shù)為:磨粒粒度125-150目;砂輪轉(zhuǎn)速25-30m/s;工件轉(zhuǎn)速0.3m/s;磨削深度<0.01mm;移動速度0.2-0.3m/min,縱向進磨量0.025-0.05mm;第二步:進行細磨,其磨削參數(shù)為:磨粒粒度380-400目;砂輪轉(zhuǎn)速25-30m/s;工件轉(zhuǎn)速0.5m/s;磨削深度<0.005mm;移動速度0.05-0.1m/s,縱向進磨量0.025~0.05mm。
在磨削過程中,砂輪磨削面的狀況會發(fā)生變化,使用一段時間后,不是發(fā)生砂輪面的砂粒被磨損掉,使得磨粒的高度與粘結(jié)劑高度相等,就是發(fā)生砂輪面被磨削材料所填充,這兩種情況都會削弱砂輪的磨損能力,導致摩擦(擦光)多于磨削,此時,應對砂輪進行修整或更換新的砂輪。當采用金剛石工具修整砂輪時,工具經(jīng)過砂輪表面的橫移速度影響砂輪的最終切削作用,快速橫移能打開砂輪面,使磨粒重新變鋒利,從而提高砂輪磨削能力;與此相反,當橫移較慢時,會導致砂輪面封閉,使磨粒鈍化并引起砂輪變硬,對熱噴涂耐磨涂層,不推薦使用慢速修整法。所以,在使用金剛石砂輪磨削耐磨涂層時,保持砂輪鋒利非常重要,有利于獲得較高的表面光潔度。
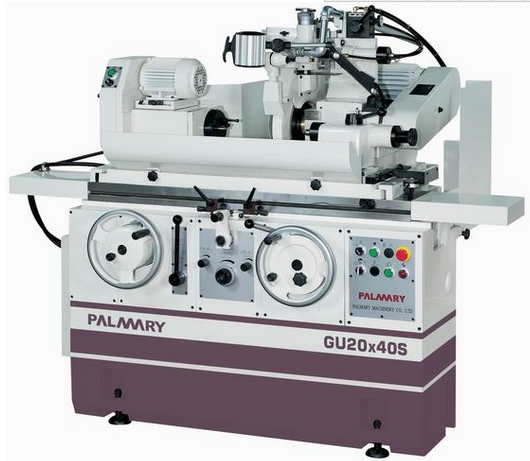
圖(3)是可以做各種耐磨涂層外圓磨加工的機床
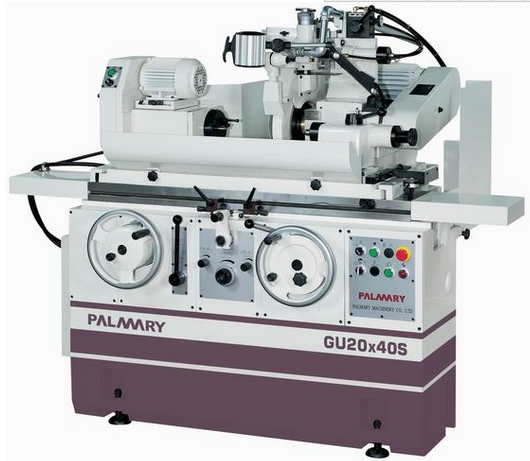
圖(3)是可以做各種耐磨涂層外圓磨加工的機床
對耐磨涂層的磨削一般推薦采用濕式磨削,如果采用適當?shù)谋Wo措施,也可采用干磨削。但是,濕磨削的優(yōu)點要遠遠大于干磨削。濕磨削時,可以使用較硬的砂輪,且不會增加爆皮或熱裂的發(fā)生率,使表面顆粒的脫出減至最少,并且得到的表面光潔度較好,砂輪不會很快被填塞,需要的修整次數(shù)也會少。此外,濕磨削還有助于沖洗掉磨屑殘渣。磨削液的過濾和合適的濃度對表面光潔度也有影響。
總之,只要在磨削加工過程中仔細操作,就可以獲得具有良好光潔度的耐磨涂層表面。下面是確定耐磨涂層磨削工藝時需要考慮的一些因素。
1)使用較軟的、自由磨削的砂輪,可大大減少擦光和磨粒脫出的機會;
2)保持砂輪面清潔、鋒利;
3)采用正確的砂輪修整工藝;
4)進行粗磨時盡量選用粗粒度砂輪,進行精磨時要選用細粒度砂輪,如果想用粗砂輪來獲得好的表面光潔度,可能導致磨粒脫出、污染或燒焦;
5)使用輕磨削。耐磨涂層通常較薄,過大的磨削壓力可能引起涂層表面分層或表面顆粒脫出;
6)進行最后一道磨削工序時應采用無火花磨削,否則會導致砂輪面鈍化或釉光;
7)始終保持涂層受壓,通過噴涂面向基體下切才能使分層和顆粒脫出限制到最小;
8)涂層磨削工藝優(yōu)化處理。磨削參數(shù)變化對磨削速度和光潔度有較大影響,耐磨涂層表面光潔度在很大程度上取決于所選用的磨削工藝。當給定砂輪存在問題時,應進行砂輪速度、進給速度、工件速度及修整工藝。
- 上一篇:帶您了解一項涂層制作主要技術(shù)——熱噴涂 2015/2/25
- 下一篇:耐磨涂層的分類及實際應用案例 2013/8/30